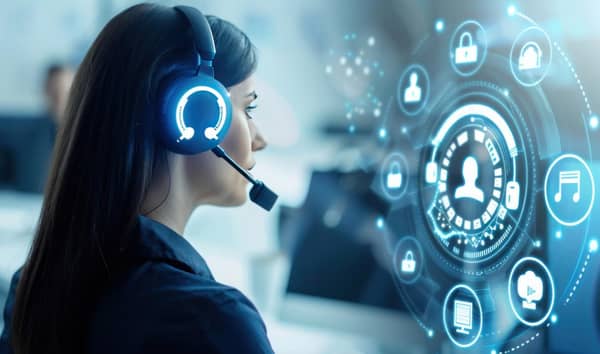
How AI Is Revolutionizing First Call Resolution (FCR) in Customer Service?
2025-02-07
In the field of industrial operations, the pursuit of product quality and cost reduction is an unending journey. One of the significant challenges in this pursuit has always been the prevalence of human errors. Mistakes in the chain of command and production processes can have far-reaching consequences, both in terms of product quality and operating costs.
Human error is one of the major causes of accidents, waste, and inefficiency in industrial operations. According to a study by the Health and Safety Executive (HSE), human failure contributes to almost all accidents and exposures to substances hazardous to health in industrial settings.
However, in recent years, the integration of Artificial Intelligence (AI), including Machine Learning (ML) technologies, has revolutionized the way industries approach these challenges.
Human error is an inherent part of any industrial process. No matter how skilled or experienced your workforce is, mistakes can happen. These errors can lead to significant consequences, including financial losses, compromised safety, and damaged reputation.
In industrial processes, even a small error can have far-reaching consequences. For example, a miscalculation in a manufacturing process can result in defective products, leading to customer dissatisfaction and returns. Similarly, miscommunication between team members can lead to delays and disruptions on the production line.
Furthermore, human error can also lead to accidents and injuries in industrial settings. Lack of attention, fatigue, and distraction can all contribute to workers making mistakes that put themselves and others at risk. These accidents not only harm individuals but also result in significant costs for the organization in terms of medical expenses, legal liabilities, and downtime.
Figure 1
To prevent human error and improve industrial operations, many organizations are turning to AI, since this technology offer solutions to mitigate the risks associated with human error in industrial processes. By leveraging AI technologies, you can automate tasks, analyze data, and make informed decisions without the limitations and vulnerabilities of human workers.
When incorporating AI and ML into their strategies and systems, organizations can achieve higher productivity, faster response times, better customer experiences, and lower costs. According to a report by McKinsey & Company, by building ML into processes, leading organizations are increasing process efficiency by 30 percent or more while also increasing revenues by 5 to 10 percent.
Implementing AI is crucial for eliminating human error and offers numerous benefits for your industrial operations:
1. Automated Quality Control
AI can significantly enhance your quality control processes by detecting defects and anomalies with highaccuracy. Machine learning algorithms can analyze images, sensor readings, and other data sources to identify deviations from expected norms. By catching defects early on, you can avoid costly rework, product recalls, and customer complaints.
2. Predictive Maintenance
AI-powered predictive maintenance can help you detect potential equipment failures before they occur. By analyzing sensor data and historical maintenance records, AI algorithms can identify patterns that indicate impending failures. This allows you to schedule maintenance activities proactively, preventing costly breakdowns and minimizing downtime.
3. Optimal Resource Allocation
The allocation of resources in your industrial processes can be optimized by AI, leading to cost savings. By analyzing data on production demand, inventory levels, and workforce availability, AI algorithms can determine the most efficient use of resources. This ensures that you allocate the right amount of materials, labor, and energy, minimizing waste and unnecessary expenses.
4. Streamlined Decision-Making
AI can analyze vast amounts of data and provide insights that support informed decision-making. By harnessing AI's analytical capabilities, you can optimize your processes, identify opportunities for improvement, and make data-driven decisions. This reduces the likelihood of errors resulting from subjective decision-making or incomplete information.
Figure 2: Applications of AI in manufacturing in 2023 (AI Multiple)
1. Data Quality and Availability
AI algorithms rely on high-quality data to deliver accurate results. It is essential to ensure that your data is clean, relevant, and representative of your industrial processes. With Tupl Industry solutions you do not need a very large amount of data to begin to operate. An inspection line can be set up with just tens of images to build the AI model. However, the more data is used as input, the more accurate the model will be, and the deep learning models will learn from any additional data, improving accuracy over time.
2. Technical Expertise
Implementing AI requires technical expertise in areas such as data science, machine learning, and software engineering.
Tupl offers no-code solutions for AI application development to help manufacturers take advantage of this emerging technology without the need to hire technical specialists or investing significant time and capital.
Tupl's software has a simple and intuitive user interface, TuplOS, that enables existing personnel and subject matter experts (SME) to build industrial AI applications for quality assurance quickly with relatively small datasets and with no programming required.
3. Scalability
As your industrial operations grow, your AI solutions must keep pace. Scalability is a fundamental consideration. As a SaaS (Software as a Service), Tupl Industry Solutions are expressly designed to scale with your business's evolving needs. Whether you're expanding operations or seeking new ways to leverage AI, Tupl's solutions can adapt to your requirements, ensuring that your AI initiatives remain effective and efficient as your business evolves.
4. Cost Considerations
Implementing AI in industrial processes involves upfront costs, including infrastructure, software, and talent acquisition. It is crucial to carefully evaluate the return on investment (ROI) and conduct a cost-benefit analysis. Tupl Industry Solutions are designed to reduce operational costs significantly. Through AI-driven quality control, predictive maintenance, and optimized resource allocation, companies can realize substantial savings. This includes lower labor costs, reduced energy consumption, and minimized resource waste.
Tupl Industry solutions are designed to help industrial and manufacturing companies automate and optimize their processes using artificial intelligence.
AI Quality Control Toolkit (AIQC) is a configurable artificial vision toolbox that allows quality control of manufacturing lines. It uses computer vision and machine learning to detect defects, anomalies, and errors in the manufacturing lines. By using AIQC, companies can reduce human error, improve quality standards, and save costs associated with rework and customer complaints.
AI Factory Toolkit (AIF) enables automation of manufacturing processes in real-time. It integrates with existing sensors, machines, and systems to collect and analyze data, and provide insights and actions for process optimization. By using AIF, companies can increase efficiency, productivity, and profitability, as well as reduce downtime, energy consumption, and human error in the chain of command.
AI Machine Control Toolkit (AIMC) allows the creation and deployment of machine control software using graphical models. It uses data engineering, feature engineering, and machine learning to provide real-time prediction and anomaly detection for machine parts. By using AIMC companies can speed up software development, reduce OPEX expenses, and ensure consistency and reliability of the machines.
Tupl Industry solutions work on a no-code MLOPs platform seeking to solve the issue of human error and cost savings in the industrial/manufacturing industry. They also enable companies to leverage the benefits of Industry 4.0 and digital transformation.
Figure 3: AI implementation in manufacturing functions (PWC)
The partnership between AI and industry is full of promise. By integrating AI into processes, we can achieve exceptional quality and substantial cost savings. The question is not if AI can eliminate human error, but how efficiently it can create a brighter, more cost-effective future for industry. AI is changing the game, and Tupl Industry solutions are leading the way in this transformation, as they are already empowering companies to reduce errors, save costs, and improve overall operational excellence.